Компания d&b audiotechnik — один из признанных лидеров рынка профессионального звука. Сегодня оборудование производства этой фирмы работает на самых престижных площадках в мире и в турах звезд первой величины. Да и артисты меньшего масштаба, как правило, не ленятся вписать d&b в свои райдеры: а вдруг повезет и выпадет шанс прикоснуться к легенде! Недавно Александр Хорев, креативный директор компании «АРИС» (официального дистрибьютора d&b в России), посетил фабрику d&b audiotechnik. Мы попросили его поделиться впечатлениями с читателями нашего журнала.
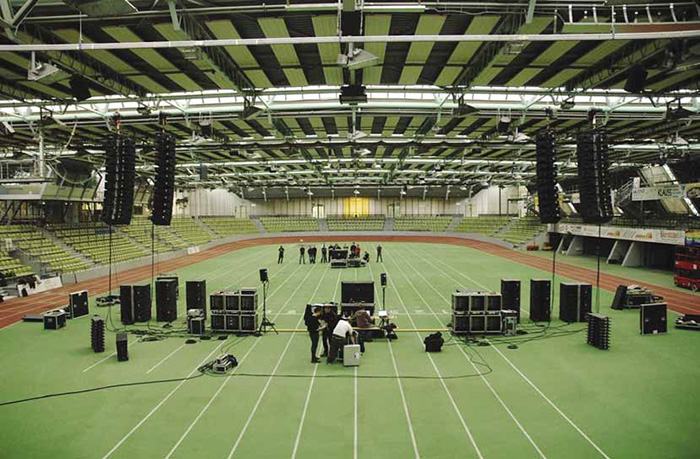
Мое знакомство с d&b audiotechnik началось задолго до того, как я стал членом команды «АРИС»; это дало мне несколько лет на выработку непредвзятого отношения. Я понимаю, что сейчас выгляжу человеком заинтересованным, но поверьте, мне ни капли не хочется рекламировать d&b. За годы знакомства с этим брендом, с людьми, его создавшими и производящими это оборудование, я привык считать, что лучшая реклама для товара — это сам товар. d&b никогда не участвует в сравнительных тестах, никогда не стремится конкурировать на уровне цены и крайне редко проводит шумные презентации. Все это не нужно. «Диэндбишники» знают себе цену. Потому что прекрасно представляют, какое количества труда, знаний и опыта стоит за каждым их продуктом. Теперь это совершенно точно представляю и я. И мне нет нужды ничего рекламировать. А вот рассказывать о том, как появляется на свет превосходный звук d&b, теперь могу часами. Возможно, прогуливаясь по пригороду Штутгарта, я подцепил тот самый вирус немецкого взгляда на технику, который заставляет людей видеть не только функционал продукта, но и красоту заложенных в него решений.
Как добиться совершенного звука? Уверен, большинство инженеров-конструкторов знают ответ на этот вопрос. Как-никак индустрия работает на полную мощность не одно десятилетие. Сделать идеальную колонку в действительности нетрудно. В единственном экземпляре. А вот тиражировать ее в промышленных масштабах — совсем другое дело. Как минимум, это очень дорого. Поэтому позволить себе наивысшее качество может лишь небольшое число компаний, обладающих достаточно серьезным авторитетом, что дает право просить за продукт максимальную цену. Предлагать рынку качественный товар на самом деле непросто. Дешево хорошо не бывает. Стоимость бренда должна покрывать расходы на тщательную разработку и прецизионное изготовление.
Итак, для производства максимально качественного товара необходима максимальная повторяемость. Без повторяемости усилия конструкторов идут прахом, а точнейшие расчеты специализированного ПО превращаются в профанацию. Все колонки должны звучать одинаково, ровно так, как это предполагал гений конструкторской мысли. Поэтому на d&b производство находится под тотальным контролем.
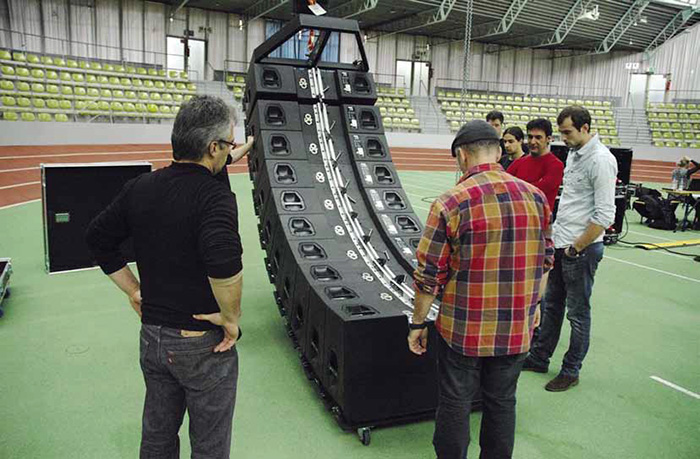
«У нас тут действует два правила, — говорит наш экскурсовод Тим Фрювирт напороге фабрики. — Ничего не фотографировать и ничего не трогать руками. Я покажу вам весь производственный процесс, за исключением департамента исследований и разработок, куда вход запрещен не только гостям, но и большинству сотрудников фирмы».
Что ж, это понятно. Репутация стоит слишком дорого, поэтому из стен R&D тут выходят только законченные решения, проверенные на все 100%. На пути к серийному производству разработчики делают множество прототипов, которые, как правило, заканчивают свой жизненный путь в огне корпоративных барбекю, периодически проводимых компанией за главным корпусом. «Возможно, в этом мангале лежит самый дорогой пепел в мире», — шутит Тим. И скорее всего, он прав. Создание каждого прототипа обходится весьма недешево.
Как разрабатывают оборудование в d&b — это тайна, покрытая мраком неизвестности. Одно могу сказать точно: порой из стен R&D выходят действительно гениальные решения. Хотите пример? За последний год компания вдвое увеличила производственные площади и количество сотрудников. И это в период общеевропейской стагнации. Очень серьезный успех. А «виной» тому новая разработка — акустика V-серии, которая просто взорвала рынок средне-форматных туровых систем. За первые полгода после выхода новинки d&bпродала более 8000 кабинетов этой серии. В какой-то момент даже были проблемы с удовлетворением покупательского спроса. Что же такого необыкновенного компания представила миру? Обычный пассивный кабинет. Каждый такой кабинет питается одним каналом усиления, в нем минимум электроники, но при этом V-серия обладает реально выдающимися характеристиками. Например, четко контролируется диаграмма направленности по горизонтали, вплоть до 250 Гц. Для пассивных кабинетов это существенное достижение. По этой части у V-серии нет аналогов. Обычно таких характеристик добиваются при помощи сложной электроники. А тут все работает за счет законов физики, то есть благодаря расположению динамиков и конструкции кабинета. Здесь нечего настраивать, следовательно, сложно что-то испортить. За это V-серию и любят прокатчики по всему миру. Минимальное время на подключение, максимально качественный результат.
В общем, в мощности умов инженеров d&bсомневаться не приходится. Вопрос в другом: как реализовать их замысел на производстве с максимальным качеством и максимальной повторяемостью? Ответ простой — тотальный контроль на всех стадиях процесса. Первый входной контроль — равномерность просушки фанеры. Если фанера просушена неравномерно, есть риск получить на выходе кабинет со смещенным центром тяжести, что приведет к отклонению всего массива от заданных координат. Честно говоря, это объяснение меня немного удивило. Отклонения в один-два градуса имеют значение для NASA. Но линейный массив…
Однако именно так достигается пресловутая повторяемость. Далее станок с ЧПУ раскраивает листы фанеры в соответствии с техническим заданием. «Например, нам нужно изготовить партию кабинетов серии J, — объясняет Тим. — Компьютер рассчитает, сколько и каких деталей нужно для всей партии, и раскроит листы фанеры так, что отходов будет минимум». В том, что фанера будет идеально раскроена, сомневаться не приходится: робот не ошибается, не устает и не имеет своего мнения относительно того, как сделать лучше.
А теперь представьте себе, что некая персона заказала партию кристаллов Swarovski и теперь сидит и пристально разглядывает каждый экземпляр под микроскопом. «Этот хорош, а этот, пожалуй, пошлите обратно». Идиотизм? Ничего подобного. Точно так же на d&b проверяют каждый динамик, полученный от поставщиков. Как вы понимаете, динамики эти — далеко не китайский no name. И тем не менее, каждый динамик проходит тест на предмет соответствия заданным параметрам. Мало того что все динамики изготовлены по спецификациям d&bсамыми известными мировыми производителями, так еще и некоторая часть из них отправится обратно после проверки на специальном стенде. Иначе нельзя — максимально возможная повторяемость.
И так во всем. Тотальный входной контроль проходит каждая деталь. Под таким же контролем находится и сам процесс производства. После каждой операции на сборочном конвейере будущая колонка d&b вновь и вновь подвергается придирчивому обследованию. Складывается впечатление, что в ходе изготовления акустических систем на проверки тут тратят больше времени, чем на работу с шуруповертом.
Перед входом на линию сборки усилителей нас просят надеть на обувь особые стремена, предотвращающие появление статических разрядов. Это обязательное правило для всех посетителей. Сотрудники фабрики работают в специальной обуви. Цех по сборке усилителей светлый и немноголюдный. Персонал в основном женский. Мужчине на такой кропотливой работе было бы трудно, поэтому представители сильного пола все больше заняты на сборке 100-килограмовых J-сабов. После сборки каждый усилитель отправляется на «прошивку», затем обязательно тестируется несколько часов с максимальной нагрузкой. К слову сказать, знаменитые D6 и D12 доживают своей век. На смену им идут монстры эры D, которые будут представлены широкой публике на следующей франкфуртской выставке. «Для нас переход на D-класс был крайне непростым, — рассказывает Тим, стоя рядом с одним из новых изделий. — Усилители D-класса обладают целой массой преимуществ, но нам было важно, чтобы наравне с этим они ничего не потеряли в качестве звука. А конкурировать по этой части, например, с D12 крайне сложно». Что ж, дождемся Франкфурта и сами все увидим. Точнее, услышим.
На одной из лестниц Тим попросил нас подойти к окну: «Видите нагромождение ящиков на крыше соседнего здания? Так мы испытываем качество покраски кабинетов. Эти тестовые образцы лежат тут уже несколько месяцев под солнцем и дождем, в жару и холод. А мы следим за тем, насколько долго краска продержится в неблагоприятных условиях». Хм… Даже такой фактор, как долговечность краски, тут стремятся взять под контроль. Впрочем, для турового оборудования этот фактор далеко не последний.
В заключение экскурсии нас приводят на склад, где хранятся комплекты оборудования, которое d&bиспользует на своих известных обучающих семинарах и воркшопах. Наверное, так выглядит рай для прокатчиков. Огромное помещение заставлено оборудованием различных серий. «А вы занимаетесь прокатом?» — раздается вопрос из аудитории. «Нет, — улыбаясь отвечает Тим. — Если мы будем заниматься прокатом, нам прострелят ноги. Это бизнес других людей. Мы разрабатываем, производим и обучаем. Иногда мы оказываем системную поддержку прокатным компаниям в больших турах, но только на уровне консалтинга». Такой вот джентльменский договор, как в старом анекдоте: d&b не прокатывает оборудование, прокатчики не производят d&b.
По итогу могу сказать, что я не заметил на фабрике d&b ничего сверхъестественного. Производства других фирм, которые мне доводилось видеть, выглядят примерно так же. Вопрос в другом. Насколько тщательно они контролируют все факторы, способные повлиять на качество звука? Ведь именно от этого зависит, насколько точно инженерная мысль будет воплощена в продукте. От этого зависит, насколько характеристики системы будут близки к расчетным.
По большому счету, самый главный вопрос — как далеко производитель готов зайти по пути к совершенству. Похоже, d&b может идти по этому пути бесконечно.